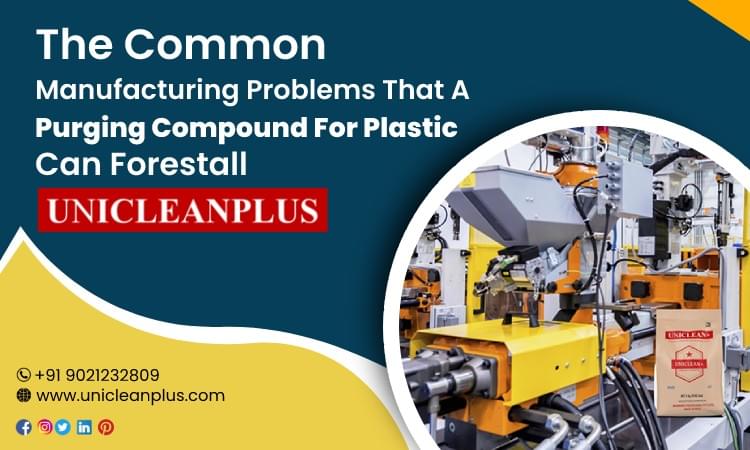
For thermoplastic processors, It is essentially vital to use a purging compound for plastic. These purging compounds have a specific design for operational processes and parameters and can make it possible to have a competitive edge over the competitive manufacturing industry. It is noticed that the build-up of carbon in screw and barrel assemblies and die sets has an immense effect on the efficiency of the process, rate of scrap production, die life and the maintenance of equipment. If there is a reduction in colour and polymer change over time using a purging compound, it is possible to have enhanced operational margins.
Other manufacturing problems can have solutions using purging material for injection moulding of reputed make. Let us have a look at some of those.
Colour Contamination
A thermoplastic process can require a lot of investment to finish a colour change or return material to virgin transparent polymer status. The speed of a colour change can be impacted by shade type, machine and process utilized, and polymer consistency. Shades impregnate the machine when handled for a long production run. While injection moulding machines are fitted with a hot-runner or a stack mould, the colour change could be complicated because of the intricacy of the actual device. Any region where polymer flow is absent can increment colour contamination issues.
Using a purging compound that is viable with your polymer and viscosity will assist you with saving investment while playing out the colour-changing process.
Material contamination
Material defilement typically follows a distinction in chemistry. It also happens due to added substance content, viscosity, explicit gravimetry, or handling temperature. For instance, a contrary polymer might flow over one more material without clinging to it. If this happens, a heavy compound structure is complicated to empty with a light chemical structure. Contrariness will produce contamination, mechanical modification, or polymer change for a period. Scrap parts can't be reused because of the presence of a contradictory polymer, which brings about a misuse of polymer, time, and energy.
Cleansing mixtures, because of their flexible processing range and further developed polymer similarity, permit machines to accomplish quicker material changes without the event of defilement from a past polymer or inconsistent polymers.
Shutdown material
Halting the machine with a standard polymer as a closure material can make long residential times. A polymer is then exposed to a halt that works with heat pressure and extensive oxidation. Therefore, polymer degradation happens. Also, heat pressure and closure material straightforwardly corresponded with the size of the machine. When a colossal machine's heaters are closed down to arrive at room temperature, material shrinkage pulls all deposits from the barrel's surface. This is an essential driver of enormous residue development that entangles machine restarts.
The use of proper purging material will decrease the negative outcome of shutdowns.
UNICLEANPLUS is the ideal organization to contact to have a purging compound for plastic and avoid such manufacturing problems. They also offer purging compounds free sample. Call them at +91 9021232809 to place your order.
Source from: https://unicleanplus.wordpress.com/