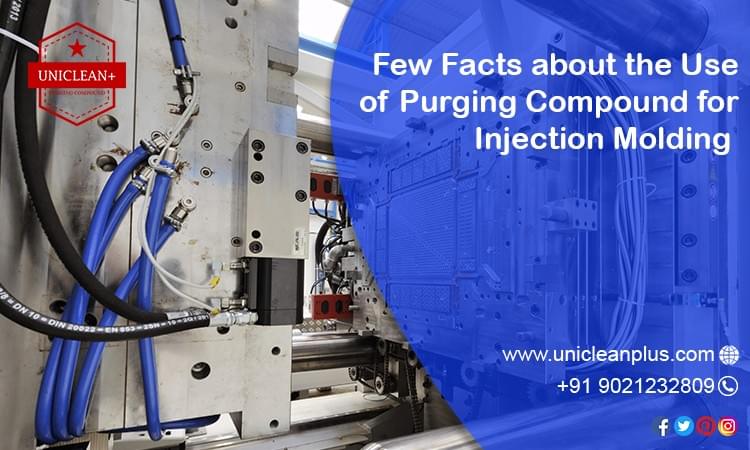
You may have noticed that injection molding organizations use resin or regrind to purge their machinery when there is a need to have colour change or carbon removal. Having such a process in place can lead to expensive waste and loss of production time. Instead, if they use the best purging compound for injection molding and follow the best practices and procedures, they can avoid such wastage and loss of time.
When one requires to clean using purging compounds
It is often necessary to use a purging compound when there is a colour changeover. It is a challenge that almost all moulders face. The changeover can take valuable time and make the spending of money to cover the cost of labour and wasted material. One of the key responsibilities of moulders is to reduce such losses. They can use purging material for injection moulding when they need to eliminate cross contamination bubbles, un-melted resins, prematerial contaminants and degraded residue from the barrels of the machine. The use of a purging compound is much more cost-effective than using virgin resins for purging.
The ideal way to purge injection molding machines
At the start of the purging process, it is wise to make certain that the injection unit stays in a retracted state and that the screws and barrels do not have anything. It is necessary to pour one or two barrels of the cleaning compound into the feeder. It is necessary to clean the nozzle and the sprue bushings.
The screw needs to be in a completely forward position, and the backpressure needs to have an increment to the maximum level. As the purging compound begins to come out from the nozzle, one can increase the screw speed to the maximum safe level. It is wise to reduce the backpressure when the compound that comes out is almost clean.
At this point, one can retract the screw and perform a short, high-velocity injection. If there are still traces of contaminants there would be a requirement to put an identical amount of purging compound into the feeder and continue the entire process.
Finally, one needs to change the purging compound with the resin that will run in the injection process. It should be done at top pressure and maximum safe screw speed. It is also necessary to set the screw completely forward.
The advantages of purging
Injection moulders can enjoy various benefits after purging the injection molding machine. There will be lesser scrap, less build-up of carbon, and avoid colour hanging in the tool. There will be a reduction in colour-changing time, and overall changeover time. There will be a decrease in downtime.
If you desire to use the best purging compound for injection molding, it is wise to contact UNICLEANPLUS. They make it possible to have free samples of purging compounds to decide the purchase of the ideal purging material. Call them at +91 9021232809 to request a free sample or to place your order.
Related Read: The Issues Faced During Molding And The Way Out