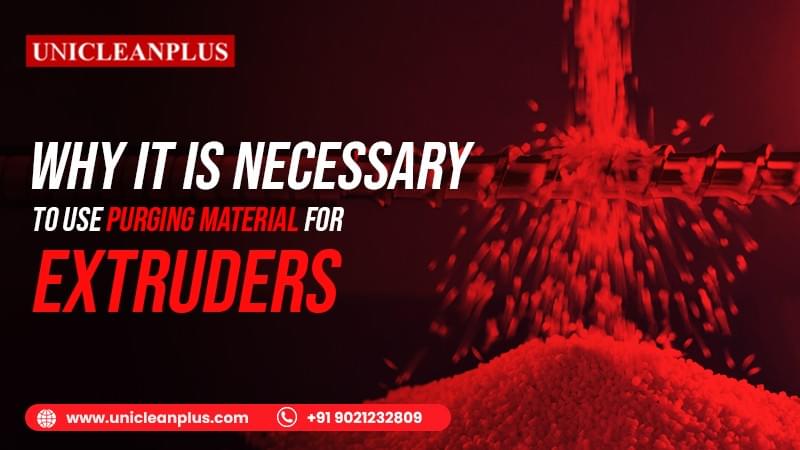
Generally, we notice that the use of purging compounds happens mostly for injection moulding. This happens due to the design of equipment and as the process of injection moulding is a cyclic one where extrusion is continuous. Then also the use of purging material for extruder has its benefits. Let us have a look at some of those.
The reasons for use of purging material for extruders
There are various reasons for the use of a purging compound for extruders. We have listed a few below:
It is easier and faster to have colour and material change using a purging compound rather than using a litre of virgin material through the extruder to clear out the earlier material. It is also noticed that there can be effective removal of persistent carbon and deposition of colour, this is not possible by using ordinary resin.
The use of purging material can relieve one from the necessity of screw-pulls. If it is somehow necessary, the use of a purging compound can reduce the time and effort required to overhaul the machine.
It is possible to use purging compounds for various natures of the extrusion process, The common use of purging compounds is in profile extrusions and compounding as there is a frequent necessity for changeovers and the variation of resins, colours and additives.
There are reputed manufacturers of purging compound who offers free sample so that it is possible to decide which compound is ideal for use in extruders and then place a bulk order.
The process of purging extruders
We can say that purging the screw and barrel of an extruder is an easier process. It becomes more problematic when there is the use of more mixing elements. Generally, there needs to be the use of one to three containers of purging material to successfully clean an extruder. It is possible to estimate the amount of purge necessary according to the screw diameter and how complex the purging application is.
To maximise the excellence of the use of a purging compound it is necessary to feed it slowly so that one can ensure that all regions are full. As the purging compound starts to come out of the machine, the screw speed can increase to the maximum safe rpm. It is necessary that during the purge one stops the screw and let the purging compound settle into some dead area. After some time, it will be good to start the screw rotation slowly and then again to maximum speed. This stop-and-go purging is called disco purge. It offers a high changing environment of pressure and agitation allowing the working of the purging compound to be the best. One needs to continue this process until the purging compound comes out clean.
If you wish to purchase the best purging material for extruder after using a free sample it is wise to contact UNICLEANPLUS. They make it possible to have the best quality purging compound at a competitive price. Call them at +91 9021232809 to request a free sample or to place your order.
Suggested Read: www.unicleanplus.wordpress.com